Various risky steps and procedures are doing handling of material. Manual methods contribute a lot to risk factors like health and different injuries which result in a massive cost of medical treatment.
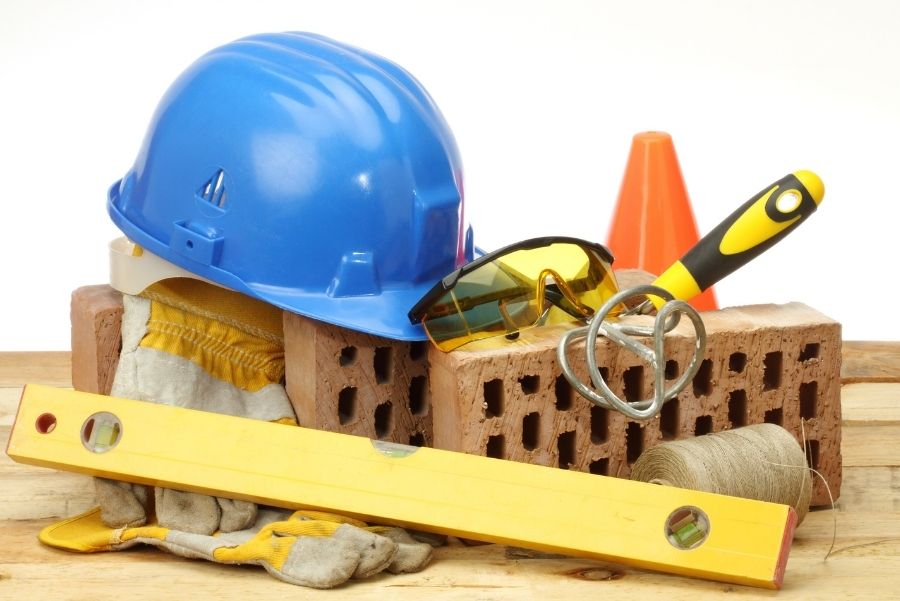
Productivity may decline due to unsafe working, leading the industry to the era of the black period. It will indirectly affect the employee, and confidence will shatter, he/she may feel less worthy or useless after such events. So, for an organization following safety measures are necessary to ensure safe handling of material:
Absolute practice strong roots
Complete training acts as the pivot in the success of any operational task. Material handling devices require trained operators who can operate them without any ambiguity. For this purpose, certified employees can help in better handling of material. It will have the following features:
- Employers should know about pressure requirements require by machines to outperform.
- Working principles of different carriers & conveyor machines
- Equipment is fragmented into different sections, so knowledge of proper installation is necessary.
- Understanding of different modes and functions of electronic devices.
- Hazards result from manual handling.
Safeguards outfits & accessories
Specific accessories and outfits can protect a worker from any injury. The organization must consider the safety of workers before work. The organization must provide worker safety accessories like:
- Head can be protected by hats and helmets made up of strong material to protect from brain injury.
- The body can be covered by wearing thermal-free suits or other kinds of cases based on work and organization. An employee can doff himself in a protective dress. The dress should be breathable and allow the passing of air in and out. It must be comfortable.
- Face the most crucial part of the body, which is always exposed to everything. Using Goggles can protect it, an inhalator and a respiratory mask, and full sheets available for protection.
- Audacity refers to hearing ability, which the loudest noisy environment can exploit. Here earbuds and muffins can protect one’s hearing ability.
- Limbs refer to the hand, foot, legs, and arms. The specific protective dress is also available like knee pads, gloves, legs, arm wrapper, etc.
Consider Ergonomic Factors
Those factors which are causing harm to humans must be minimized. Key aspects are gesture and movement with posture, repetition of motion, specific actions like uplifting of material, etc. These occur mostly in manual handling; automated handling facilitates the employee and industry both. Timely screening of all ergonomic factors is necessary for reducing injuries and harms.
Utilization of the Latest Equipment
The organization can upgrade their old equipment and devise to the most developed technologies like conveyors, industrial trucks, and cranes. This equipment work on the principle of artificial intelligence programmed and designed by software engineers. It could enhance the safety of employees during material handling. Organizations and industries can experience infinite work and production by utilizing the latest automated gadgets and equipment. For example, Deck Builders Wollongong workers can complete a single project in less than a month.
Pre-Inspection
It is just like a demo, and a trial activity performed to check the working condition and probability of certain diseases. In material handling, an experienced safety manager can visually inspect the procedure and gadgets to ensure workers and the organization’s safety. It includes the following features:
- Checking operational manuals to ensure no misguidance is provided.
- Inspecting internal and external surfaces of machines to ensure no leakage or crack or porosity will occur.
- Lubricating the old equipment for smooth performance.
- Cleaning of dusty and rusty components.
- Connecting dots like cables and plugs.
- Checking working and functionality of risk determining devices like a fire alarm, short circuits detector, etc.
Employ Health Screening
Regular and timely health screening is necessary as most of the work is done by the employees, especially the labour class. They pass through some phases like different postures, twisting, and uplifting of material during material handling. It sometimes causes fatigue. If there is a considerable workload, then there should be some substitute. There should be a health screening department in every organization where an employee’s health must be checked promptly.
Conclusion
Whether it is manual or automated handling of material, it requires some safety measures to be taken. Although technology is advancing every day, it doesn’t guarantee safety. So, proper guidance and training are crucial for employees who are handling the material.
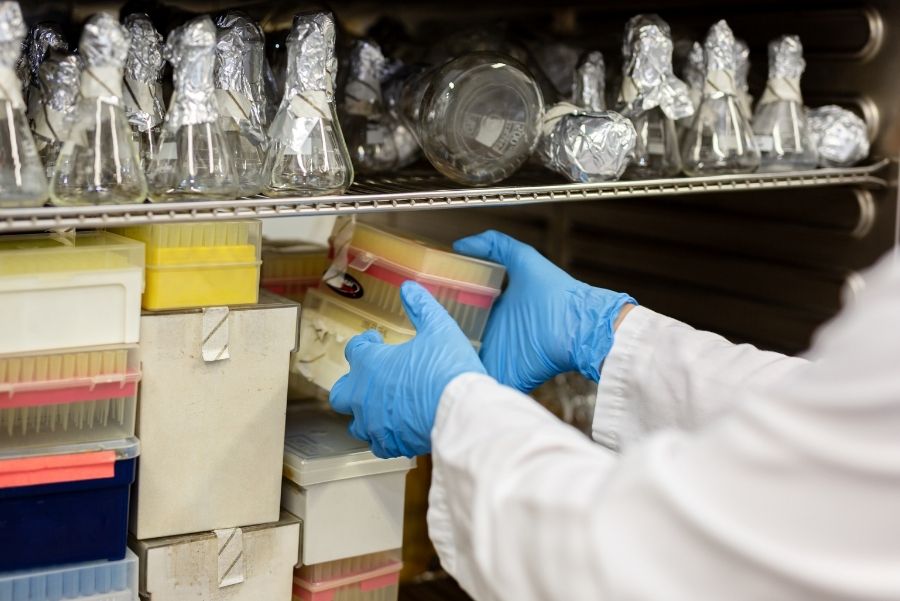